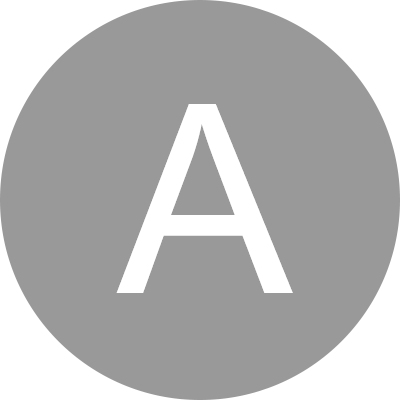
To prevent problems, replacement of brake discs/pads by trained professionals should only be allowed.
In the replacement process, the following matters should be observed in principle:
Brake disc
Only the entire shaft is allowed to be replaced, paying attention to the direction of rotation if necessary.
Correctly center and fix with the specified torque in the specified order.
IMPORTANT: Check the face side pendulum.
Replace the brake discs with new Otto Zimmermann brake linings or other approved brake linings (ECE R90 approved).
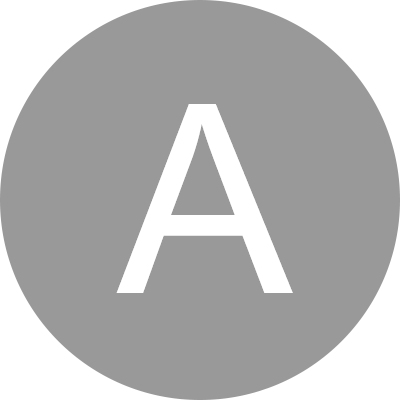
The following running-in instructions are recommended to ensure proper functioning of the brake disc/pad system:
Section where the running-in process is performed: the section where the following driving maneuvers are allowed under the premise of complying with the provisions of the Road Traffic Management Law.
Avoid sudden braking for the first 300 km after replacing the brake disc.
Through moderate running-in, the temperature of the brake disc can be gradually increased under the premise of ensuring that there is no sudden increase in temperature, and the coordination between the friction surface of the brake disc and the friction surface of the brake lining can be realized.
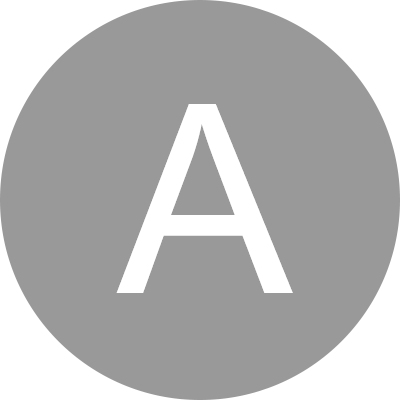
If vibration occurs under thermal load, it is usually caused by "brake disc deformation. If, in addition, different measured values are obtained when measuring the brake disc thickness, the following diagnostic results seem to be confirmed: brake disc twisting, brake disc "wobbling", brake disc out-of-round, brake disc deformation, etc.
But the real cause of this phenomenon is different: the current generation of brake linings is designed for friction. When the brake disc/brake lining system is correctly engaged, a very thin and homogeneous layer of brake lining material is formed on the brake disc friction surface due to diffusion processes. As a result, more or less of the same material is present in the edge regions of the two friction surfaces (brake disc and brake lining); it is possible for a hierarchical transition (diffusion) of material particles to form in both directions. As a result, the chemical bond between the casting material and the brake lining material may be broken or re-formed.
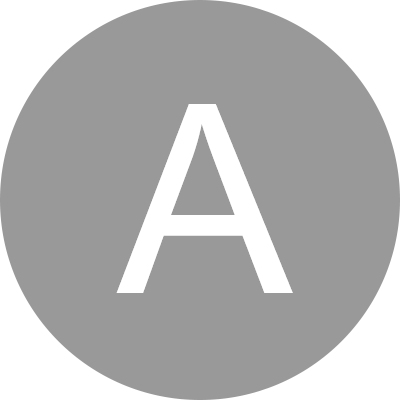
HAICHEN brake discs are usually made of gray cast iron (with flake graphite) of different quality; the brake discs should correspond to the material of the original spare part.
The casting quality used contains only very small amounts of alloying elements with a corrosion-inhibiting effect. If products made from such materials are exposed to adverse weather conditions (e. g. rain, fog, high humidity, melting snow or de-icing salts), the product will rust after a short period of time. In order to counteract this corrosion, all HAICHEN brake discs and brake drums are in principle coated with an anticorrosive coating.
Most of the products in HAICHEN company's product portfolio are coated with "Coat Z" corrosion-resistant coating. This ensures that the corrosion tendency of the contact-free region of the brake lining is significantly reduced.
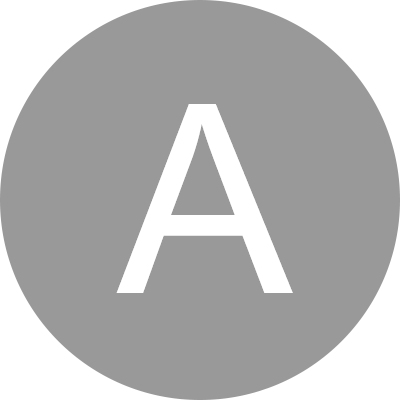
Based on the latest developments in the field of casting technology, it is ensured that the stress-free state of the blank is achieved in the foundry by controlling the cooling process after casting. As a result, it is now possible to dispense with the costly annealing of the blank or semi-finished part (the temperature is slowly raised to the annealing temperature, held at this temperature for several hours, and then slowly cooled again).
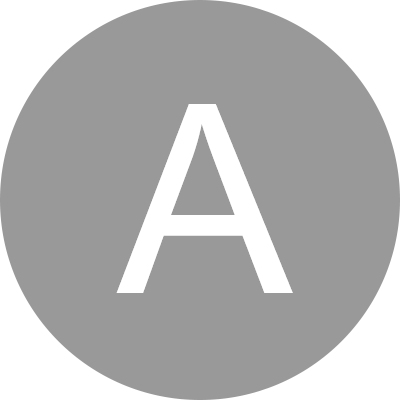
In principle, HAICHEN brake discs (standard and perforated) are made in strict accordance with the dimensions of the corresponding original spare parts and the materials used (in accordance with GVO, ISO9001, ISO/TS16949 standards).
The perforated models have been tested by TÜV Nord in terms of functionality, operational reliability and wear resistance and have been approved by the German Federal Automobile Administration for use as specified in production vehicles; the brake discs meet the general requirements related to mechanical and thermal loads when used for the intended purpose.
Brake discs used in retrofit vehicles and vehicles participating in motorsport (or the like) are often required to meet higher requirements in terms of mechanical and thermal load capacity. The same applies to the brake lining.
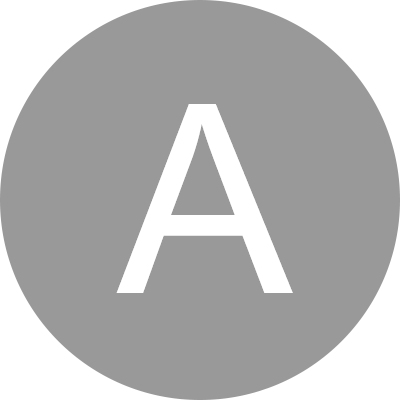
In any case, you should look for the nearest professional repair shop. Diagnosis shall be made only after vehicle identification has been completed on site.
The most common causes are listed below:
Installation errors due to non-compliance with assembly regulations
Using the wrong brake lining
Brake system overload
Wheel imbalance
Steering system damage (e. g. worn tie rods)
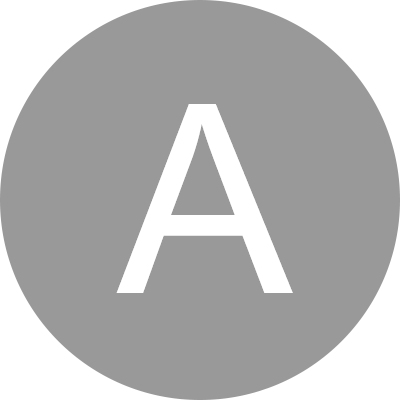
Possible brake noises are not generated by the brake disc itself! The "culprit" that causes such resonant noise is other components of the brake system that act directly or indirectly on the brake disc. The brake lining shall be the first component that generates brake noise. When the brake lining fails to match the brake disc optimally due to its composition, or when its assembly process does not completely meet the requirements of the brake disc, it will cause brake noise. Another cause of brake noise is foreign matter embedded between the brake disc and the brake lining.